What are the methods for heat treatment of straight seam steel pipe?
First of all, the layout design of technical molds should be reasonable, the thickness should not be too different, and the shape should be symmetrical. For molds with large deformation, the deformation rules should be grasped, and the machining allowance should be reserved. For large, fine and disordered molds, the combined layout can be selected. For some fine and disordered molds, pre heat treatment, aging heat treatment and quenching and tempering nitriding heat treatment can be selected to control the accuracy of the molds. When repairing defects such as sand hole, air hole and wear of the mold, repair equipment with small thermal impact such as cold welding machine shall be selected to avoid deformation during repair.
Fine and disordered molds shall be pre heat treated to eliminate the residual stress during machining. For fine and disordered molds, vacuum heating quenching and deep cooling treatment after quenching shall be selected as far as possible if conditions permit. On the premise of ensuring the hardness of the mold, pre cooling, staged cooling quenching or warm quenching process shall be selected as far as possible.
Reasonably select materials. For fine and disordered dies, the micro deformation die steel with good raw materials shall be selected. The die steel with severe carbide segregation shall be properly cast and subjected to quenching and tempering heat treatment. For large and non cast die steel, the solid solution double refinement heat treatment can be carried out. Reasonably select the heating temperature and control the heating speed. For fine and disordered molds, slow heating, preheating and other balanced heating methods can be adopted to reduce mold heat treatment deformation.
JCOE is a pipe making technology for the production of large diameter thick wall steel pipes. It mainly adopts the production process of double-sided submerged arc welding. The products go through multiple processes such as milling, pre bending, bending, seam closing, internal welding, external welding, straightening, and flat end. The forming process can be divided into N+1 steps (N is a positive integer). The steel plate is automatically fed laterally and bent according to the set step size to realize the numerical control progressive J-C-O forming. The steel plate enters the forming machine horizontally, and under the push of the feeding trolley, the first stage of multi-step bending with N/2 steps is carried out to realize the "J" forming of the front half of the steel plate; In the second stage, firstly, the steel plate formed by "J" shall be sent to the specified position in the transverse direction rapidly, and then the unformed steel plate shall be bent in multiple steps of N/2 from the other end to realize the forming of the second half of the steel plate and complete the forming of "C"; Finally, the lower part of the "C" type tube blank is bent once to realize the "O" forming. The basic principle of each stamping step is three-point bending.
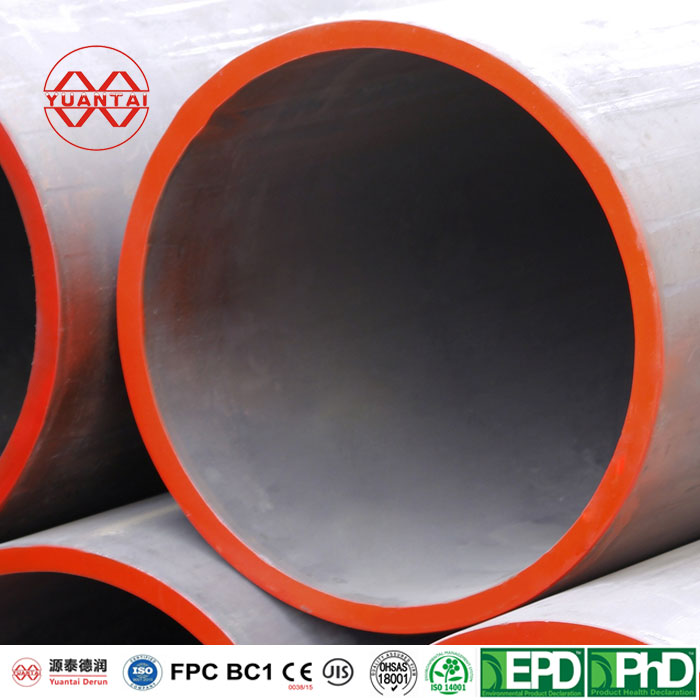
Post time: Sep-30-2022